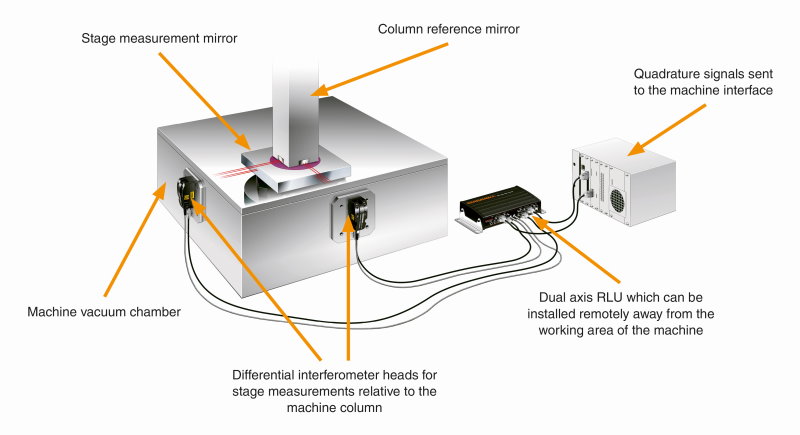
Renishaw supports ASML with bespoke laser encoder solution
Modern semiconductor technology is dependent on precise control of the various processes used in the production of integrated circuits. Semiconductor wafers are inspected after each processing step to locate problems as early as possible. This inspection requires that the whole wafer or mask area is scanned quickly so that high levels of production throughput are maintained.
The moving parts of a metrology machine include the wafer (substrate) motion stage, the detector and signal optics. The motion control systems depend on high-quality position encoder feedback to deliver exceptional positioning accuracy.
Special requirements
In 2018, ASML contacted Renishaw about a wafer stage design for its new generation of inspection systems. With its multiple degrees of freedom, the stage has complex metrology requirements. ASML had devised a position encoder hardware specification based on our RLE20 dual-axis laser interferometer encoder.
Recognized for its high accuracy, the RLE20 system is a laser position encoder designed for linear position feedback. It comprises a laser unit (RLU) and detector heads (RLDs) that interact with reference and position measurement mirrors. The differential interferometer head is directly mounted to the external wall of the process chamber and features low cyclic error and high accuracy. Some interface configurations can provide output resolutions as fine as 38.6 picometers. The system is available in multiple configurations to cater for different optical arrangements and applications including angular measurement. A standard application of the encoder is for the XY motion control of metrology machines.
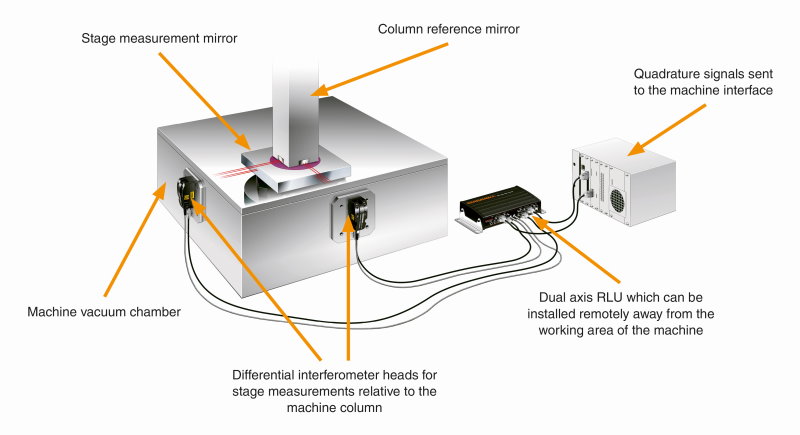
ASML had special requirements for their application that weren’t completely met by the standard RLE20 system. Details of the hardware and performance requirements were shared with us in a comprehensive specification document. The project demanded a bespoke laser encoder solution that could be delivered to a tight schedule before the start of production of ASML’s new inspection systems.
Close working relationship
Renishaw formed a dedicated project team to ensure that the new laser encoder would be ready in time. Over the following months, the teams from both companies worked jointly to evolve an achievable product specification that would meet the stage performance requirements and tight schedule. This included several face-to-face group sessions at Renishaw headquarters in Gloucestershire, UK, and ASML’s headquarters in Veldhoven, the Netherlands.
The technical collaboration relied on a close working relationship, including the disclosure and discussion of commercially sensitive details. Under NDA, we were informed about the novel aspects of the motion stage design and ASML was able to acquire deeper knowledge of the metrology aspects of the laser interferometer system. By working closely and transparently with ASML, we gained valuable insights into their specific needs and challenges. This enabled us to design and deliver an encoder that met their high standards and integrated seamlessly into their system.
The Renishaw project team set out to develop and validate solutions to meet ASML’s performance requirements, with initial deliveries to ASML commencing in 2019. Overcoming considerable technical challenges, our team adapted the current RLE20 design to create the new RLE21 encoder.
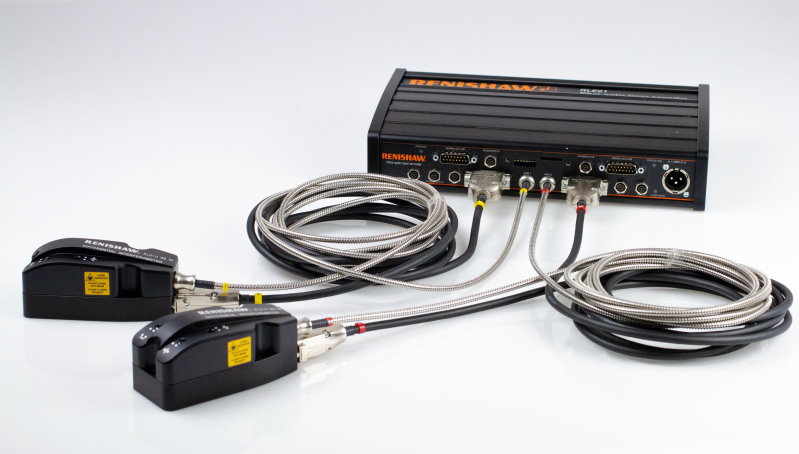
Key changes
The development of the RLE21 system involved several key changes. These include the validation of an extended optical angular range, which is important for ensuring the laser system’s signal strength over a wider range of angular misalignment. This enabled ASML to design a more complex motion system that accurately controls each additional degree of freedom of the motion stage. Precise angular measurements are also possible; these are derived from the path length difference between two measuring beams at different points of interest on the same mirror as it yaws or pitches.
Furthermore, the differential interferometer heads supplied with each RLE21 system have improved beam steerer mechanisms. These allow for finer pitch and yaw adjustment during setup. This, in turn, improves the alignment process.
ASML has also been given access to diagnostics software within the RLE21 system. This involved an electronics redesign of the laser unit and the definition of a communication protocol they could use in their front-end software. The software improves system setup and enables remote access to encoder system diagnostics.
For plug-and-play functionality, a new electronics scheme was developed with an improved offset and gain setting. As a result, an RLD detector head can be paired with any RLE21 laser unit without a system matching process. This has several advantages including reducing downtime for maintenance.
ASML required additional product testing at our manufacturing site to prove that each encoder conformed to the enhanced specification. Further requirements were jointly evolved to ensure delivery acceptance and included product identity labeling, ISO Class 4 cleanroom product and packaging compatibility and transport packaging. We invested in new equipment and processes to achieve this. As part of qualifying and introducing new suppliers, ASML implemented a detailed Long-Term Supply Agreement (LTSA), which is a binding contract for the supply of the RLE21 encoder. Following successful system testing in the Netherlands, we continue to supply our laser encoder to the ASML production facilities in Taiwan.
Future products
The RLE21 laser encoder was designed to meet ASML’s tight schedule, solve several technical challenges and improve the ease of encoder system installation and setup. The project enabled Renishaw to develop new manufacturing processes and in-house expertise for future ASML-specific product collaborations. Many of the design improvements from the RLE21 encoder project are being integrated into future products intended for our interferometric laser encoder range.