Your cart is currently empty!
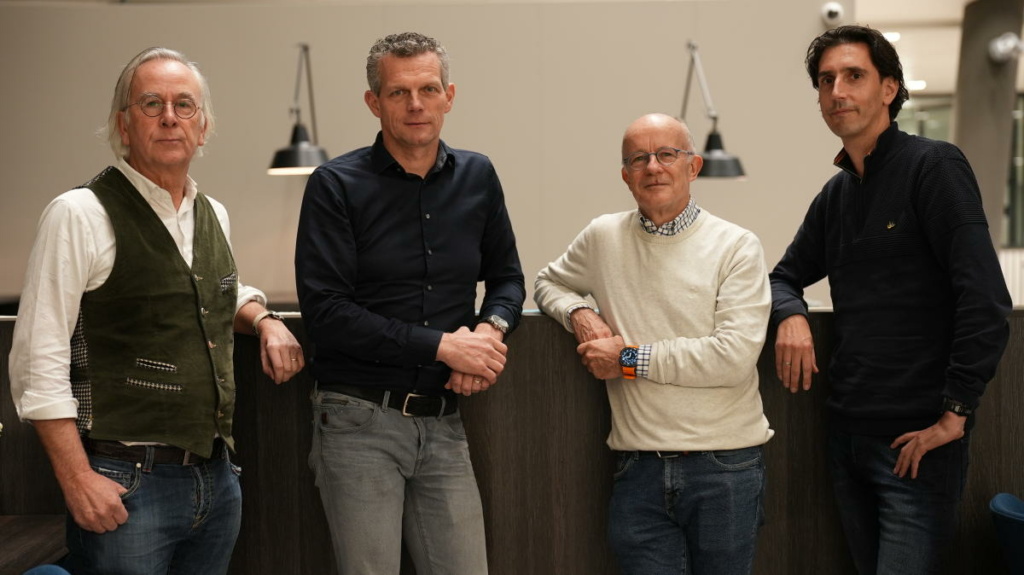
“Calculations you should be able to do in five minutes on a beer coaster”
Erik Manders and Marc Vermeulen are assuming a leading role in the training “Design principles for precision engineering” (DPPE). The duo takes over from Huub Janssen, who was the training’s figurehead for seven years. Part two of a two-part series: training, trends and trainers.
When it comes to knowledge sharing within the Eindhoven region, the “Design principles for precision engineering” (DPPE) training is considered one of the crown jewels. The course originated in the 1980s within the Philips Center for Manufacturing Technology (CFT), where the renowned professor Wim van der Hoek laid the foundation with his construction principles. Rien Koster, Piet van Rens, Herman Soemers, Nick Rosielle, Dannis Brouwer and Hans Vermeulen subsequently built on it.
The current DPPE course, offered by Mechatronics Academy (MA) through the High Tech Institute, is supported by multiple experts. The lead figures among them have the special task of keeping an eye on industry trends. “Our figureheads signal trends, new topics and best practices in precision technology,” says Adrian Rankers, a partner at Mechatronics Academy, responsible for the DPPE training.
When asked about his ‘fingerprints’ on the training, former figurehead Huub Janssen refers to his great inspiration, Wim van der Hoek. “I’m not a lecturer nor a professor with long stories. I like to lay down a case, work on it together and then discuss it. With Van der Hoek, we would all sit around a large white sheet of paper and then the problems would come to the table.”
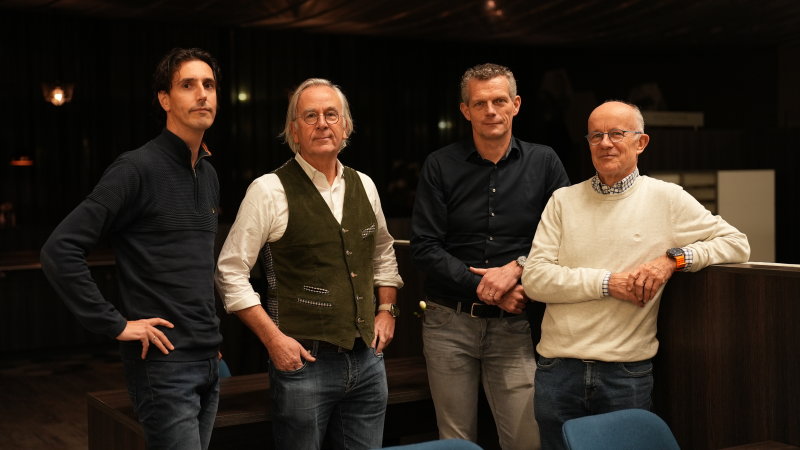
Bias and complacency
Janssen says that as a figurehead, he was able to shape the DPPE training. He chose to give participants more practical assignments and discuss those cases in class. Rankers: “Right on the first morning. After we explain the concept of virtual play, we ask participants to start working with it.” Janssen: “Everyone thinks after our explanation: I’ve got it. But when they put the first sketches on paper, it turns out it’s not that simple. That’s the point: because when they do the calculations themselves, it really sticks.”
On the last day of the training, participants are tasked with designing an optical microscope in groups of four. Janssen: “They receive the specifications: the positioning table with a stroke of several millimeters, a specific resolution, stability within a tenth of a micrometer in one minute and so on. Everything covered in this case has been discussed in the days prior: plasticity, friction, thermal center and more.”
Vermeulen: “The fun part is that people have to work together. Otherwise, they won’t succeed.”
“We push four tables together and they really have to work the four of them as a team,” Janssen continues. “Then you see some people going for super-stable Zerodur or electromagnetic guidance or an air bearing, and someone else asking: ‘What about the cost aspect?’”
Janssen notices that a certain bias or complacency is common among designers. “When there are many ASML participants in the class, they immediately pull out a magnetic bearing when we ask for frictionless movement. But in some cases, air bearings or two rollers will do. I’m exaggerating, but designers sometimes have a bias because of their own experience or work environment. With every design question, they really need to go back to the basics. They have to put their two feet on the ground and start simple.”
Vermeulen: “The simplest solution is usually the best. Many designers aren’t trained that way. I often see copycat behavior. But the design choice they see their neighbor make isn’t necessarily the best solution for their own problem. You could equally well use a steel plate instead of a complex leaf spring. It works both ways, but if you choose the expensive option, you better have a good reason.”
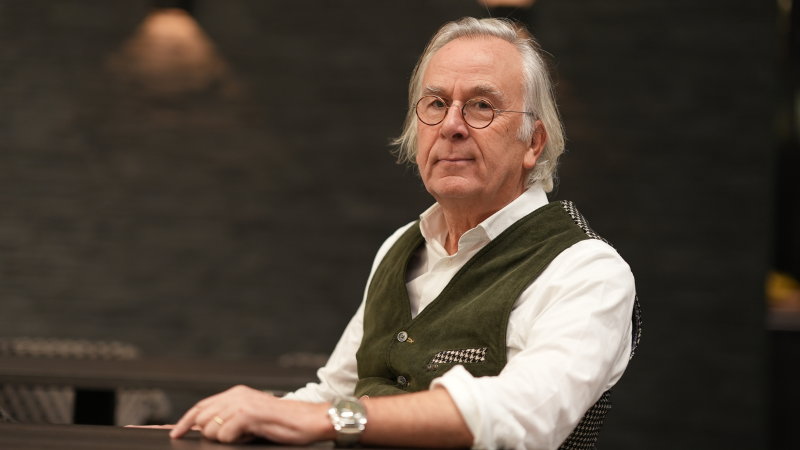
Feeling
Participants experience the difficulty level very differently, regardless of their educational background, Janssen observes. “It depends on their prior knowledge, but it’s challenging for everyone. Participants are almost always highly educated, but when they need to come up with a design, they often don’t know whether to approach it from the left or right.”
Still, he believes it’s not rocket science. “It’s not complex. It’s about calculations you should be able to do in five minutes on a beer coaster.”
It’s about getting a feel for the material. “You should also be able to quantify it, quickly calculate it,” emphasizes Vermeulen.
Janssen offers a simple thought experiment: “Take two rubber bands. Hold them parallel and pull them. Then tie them in series and pull again. What’s the difference? What happens? Where do you have to pull hardest to stretch them a few centimeters? Not everyone has an intuitive grasp of that.”
Rankers: “It’s a combination of creativity and analytical ability. You have to come up with something and then do some rough calculations to see how it works out. Some people approach it analytically, others can construct wonderful things. They may not know exactly why it works, but they have a great feel for it.”
All agree that creativity and design intuition can’t be replaced by calculation tools. “You can have a computer do the calculations,” says Janssen, “but then you still need to assess them. What if they’re incorrect? There are thousands of parameters you can tweak. It’s about having a feeling for construction, knowing where the pain points are. You don’t need a calculation program for that.”
Erik Manders: “You want an initial sketch or calculation. If you let a computer do that for you, you’re busy for days. Building an initial model takes a long time. But a good constructor can put that calculation on paper in a few minutes. If afterwards, you’re busy for an hour, you have a good sense of which direction it’s going. I think that’s the core of the construction principles course: do simple calculations, don’t make it too complicated, choose a direction and see where it goes.”
Manders observes that highly analytical people are often afraid to put the first lines on a blank sheet of paper, to start with a concept. “Often, they’re so focused on the details that they immediately get stuck. Creatives start drawing and see where it goes.”
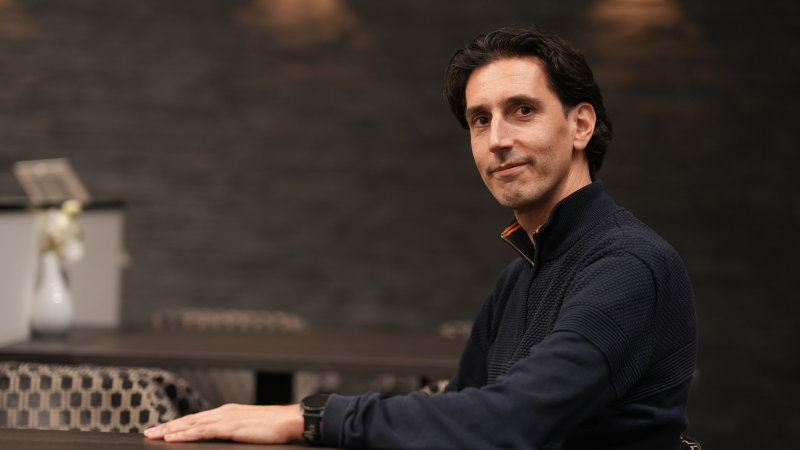
Energy
For Manders, training is a way to stay connected with the field of construction. “In my career, I’ve expanded into more areas, also toward mechatronics. But my anchor point is precision mechanics. By training, I can deepen my knowledge and tell people about the basics. It sharpens me as well. Explaining construction principles in slightly different ways helps me in my coaching job.”
He also learns new things during training. “I often get questions that make me think. When they’re really tough, I’ll come back to them outside the course. I’ll work it out at home and prepare a backup slide for next time.”
Vermeulen says he gets a lot of satisfaction from training a new generation of technicians. “That gives me energy. For the current growth in high-tech, it’s also necessary to share knowledge. That applies to ASML but also to VDL and other suppliers. If we don’t pass on our knowledge, we’ll hit a wall.”
“It’s always fun to see how Marc starts,” says Rankers about Vermeulen’s approach in training. “When he talks about air bearings, he asks participants if they use them, what their biggest challenge is, where they run into problems. In fifteen minutes, he explores the topic and knows what’s familiar, who knows a lot, who knows nothing and who’s about to work with it in a project.”
Vermeulen: “I go over the entire material without diving deep. That process gives me energy. The whole class is motivated, but the challenge is to really engage them at the start. You don’t know each other yet. But I want to be able to read them, so to speak, to get them involved. They need to be eager, on the edge of their seats.”
It’s not about the slides, Vermeulen emphasizes once again. “It’s about participants bringing their own questions. They all have certain things in mind and are wondering how to make it work.” That’s the reason for the extensive round of questions at the start. “I ask about the different issues they’re encountering. Then I use that as a framework. When a slide about a topic they mentioned comes up, I go into it a bit. That makes it much easier for them to follow. They stay focused.”
Fundamentals
Although they see opportunities to bring the content more up to date, Manders and Vermeulen don’t expect major changes in the material covered. After all, DPPE is a basic training and participants still need to learn the fundamentals. Complex concepts like passive damping are only touched upon briefly – Mechatronics Academy offers a separate three-day training for that.
Janssen teaches the participants about stiffness, play and friction. “These are crucial topics, so I spend a day and a half on them. If you don’t grasp them, you’ll never be a good designer. They’re fundamental.”
The “degrees of freedom” topic taught by Manders is another fundamental element. “That takes time. You have to go through it,” he says.
Vermeulen: “Then comes the translation to hardware. Once participants are familiar with spark erosion, for example, they need to have the creativity to also turn to cheaper solutions. We could emphasize considering the costs of production methods more during the training. If spark erosion gives you a degree of freedom in one system, you shouldn’t automatically choose this expensive production method in the next system as well. We should delve more into that translation to hardware. It’s also good to strive for simplicity there.”
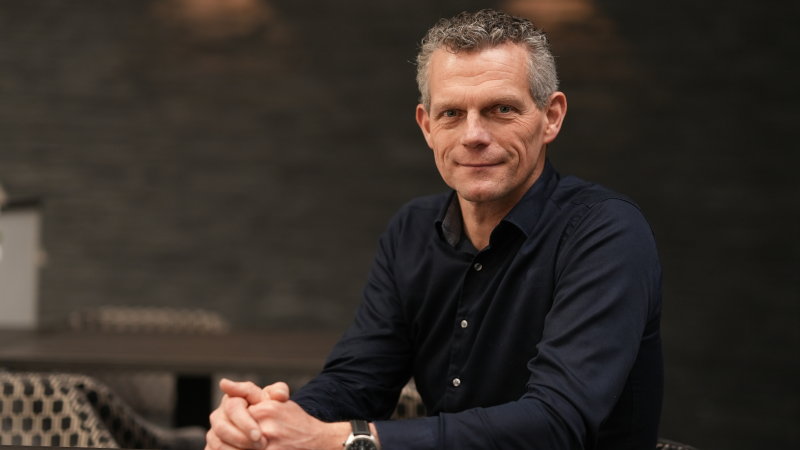
Cost aspect
Wim van der Hoek also had a critical eye for costs. Rankers: “A great statement from him was that many costs in assembly are caused by things being overdetermined.”
The terms “determined” and “overdetermined” in precision engineering essentially refer to this: a rigid body has six degrees of freedom (three translations and three rotations) that fully define its position and orientation. If you want to move that object in one direction using an actuator, you need to fix the other degrees of freedom with a roller bearing, air bearing or leaf spring configuration.
If you as a designer choose a configuration of constraints that fixes more than five degrees of freedom, the constraints may interfere with each other. Rankers: “That’s called statically overdetermined. When you’re lucky, it works, but only as long as everything is neatly aligned. The people doing that have ‘golden hands,’ as Van der Hoek put it. But you really have to be careful that your neat alignment doesn’t change, for example due to thermal expansion differences.” Especially the gradients and differences in expansion of various components play a big role.
Rankers: “Of course, it’s impossible to perfectly align everything. It also changes over time during use. The clashing constraints cause internal forces to arise within the object you want to hold or position. If that object is a delicate piece of optics that isn’t allowed to deform, you’ve got a big problem. That means you need to avoid overdetermination in ultra-precision machines.”
Vermeulen: “If you design it to be better determined, it’s easier to assemble, thereby reducing costs.”
Rankers, too, recognizes that the cost aspect should receive more attention. He thinks guest speakers could enrich the training with practical examples, showing affordable and expensive versions. Vermeulen immediately offers an example of guiding a lens. “If you make a normal linear guide, the lens sinks a little on the nanometer scale. You can compensate with a second guide, but then the solution might be twice as expensive and twice as complex. Is that really necessary? So as a designer, you can challenge the optics engineer: ‘You want to make it perfect, but that comes at a high cost.’ We need to pay attention to these things.”
This article was written in close collaboration with High Tech Institute.