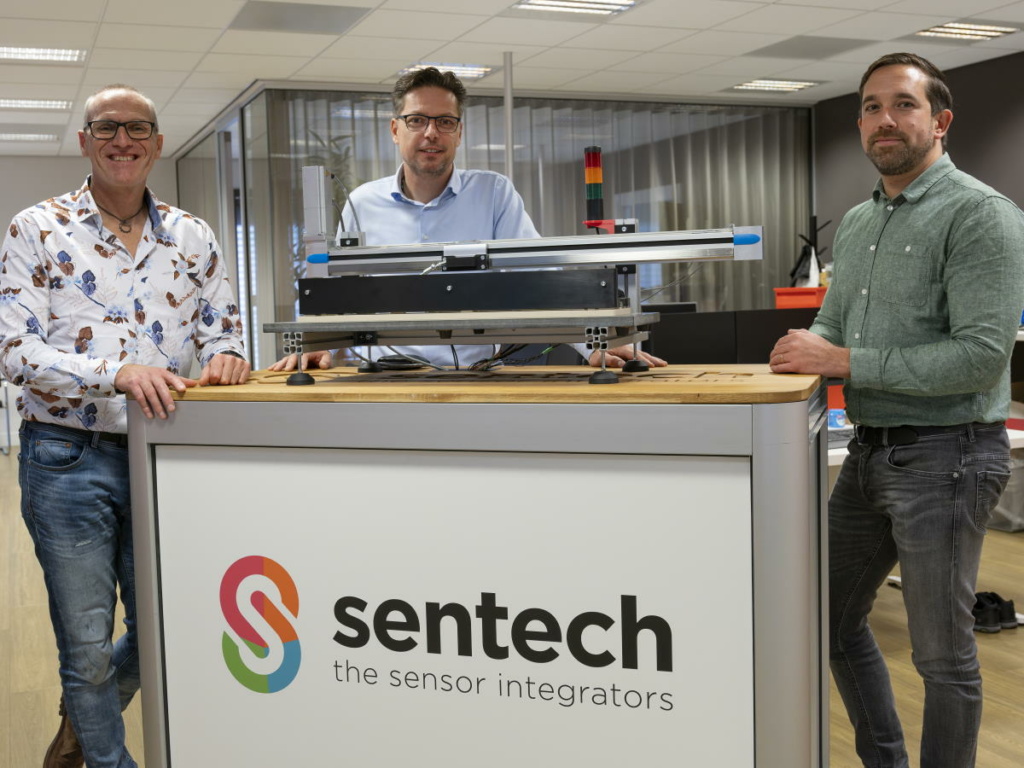
Challenging physics, challenging collaboration
Component Management has grown into an important discipline at ASML, covering a large number of product categories. Mario Creemers is responsible for the sensor portfolio. Together with a colleague, he manages a database with more than 1,600 different components, from monoparts such as NTCs to off-the-shelf camera assemblies to high-end encoder and measurement systems. âWe consult with our engineers about the selection of components for the functionality theyâre developing, while taking into account as much as possible the QLTC guidelines for quality, logistics, technology and cost. We also have to deal with possible end-of-life issues and compliance, concerning REACH, RoHS, conflict minerals and, exploratory, PFAS materials.â
For various sensor challenges, Creemers calls on Sentech in Nieuwkuijk, since its founding in 2000 a supplier of ASML and its first-tier system suppliers. âTheyâre innovative and solution-oriented. For sensor-based assemblies, Iâve come to consider them as a co-maker.â
Over the years, Sentech has provided many sensor solutions to ASML, says account manager Peter Verstappen. âWeâve built sensor assemblies for all systems, from the PAS 5500 to the latest EXE EUV machine, following their roadmap towards better performance in terms of higher accuracy, smaller dimensions, better cleanliness and higher vacuum. For new developments, we brainstorm with ASML architects and ask the questions they havenât yet asked themselves. We do this for both relatively simple and advanced sensors, regarding their functionality as well as their integration into complex machines.â
From simple to special
One example of a relatively simple sensor concerns the refurbishment of an old system â a float switch for leakage detection turned out to be end-of-life. Verstappen: âIt wasnât a high-tech sensor, but we couldnât find a supplier. So, we had to develop our own solution in close collaboration with a manufacturer that was new to ASML. As we knew their capabilities, we didnât hesitate to introduce them to the ASML supply chain.â
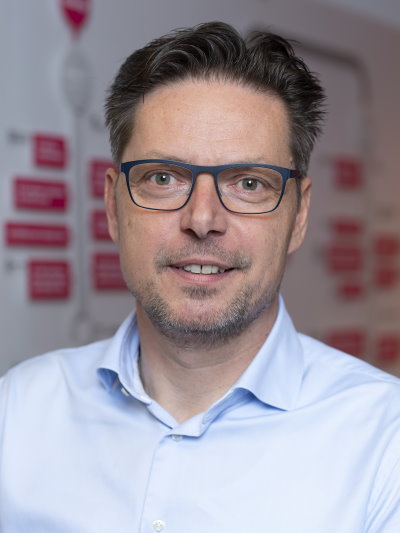
An advanced case comes from the liquid tin high-pressure vessel for the EUV source. A new sensor was required for a more accurate measurement of the vesselâs filling level. For this, the change to a sensor principle based on force measurement was considered, Creemers explains. âSpecifications differed greatly from those for standard force sensors. The sensor had to withstand high forces while having a high measurement sensitivity, as well as high temperatures in a vacuum environment.â
âThat combination didnât exist yet and in a discussion with ASML architects, the consensus was that it wouldnât be feasible,â adds Verstappen. âHowever, we werenât convinced and started looking for a suitable manufacturer. Many candidates were quickly rejected until we found a party that asked the right questions, which made us realize that they could develop and make the requested sensor.â
Old and new
Challenges can be found in the development of new systems as well as in the refurbishment of older systems. âWhen we have to build a sensor module for a PAS 5500 system, for example, we take the old technical product documentation,â Verstappen explains. âFor most of these modules, we can still supply the older designs and sensor assemblies.â But what if the components concerned are no longer immediately available? âThen we have three options. The first is commercial off-the-shelf. If the sensor is still built somewhere in the world, weâll find it. We then create an assembly around it so that it fits in the machine.â
If thatâs a no-go, modified off-the-shelf is the second option. Verstappen: âWhen we find a sensor that looks like what we need but doesnât fit exactly, we contact the engineers who have the sensor IP to show them our specs and start co-developing a new solution. For many component manufacturers, ASMLâs low-volume, high-variety profile doesnât fit their business model, but we keep looking until weâve found a supplier thatâs willing to make those 50 pieces, for example.â Creemers: âItâs essential that Sentech isnât brand dependent and can therefore search broadly in the market. Thatâs what I do myself, of course, but when I have too many things on my mind, itâs nice to be able to use Sentech as an extension.â
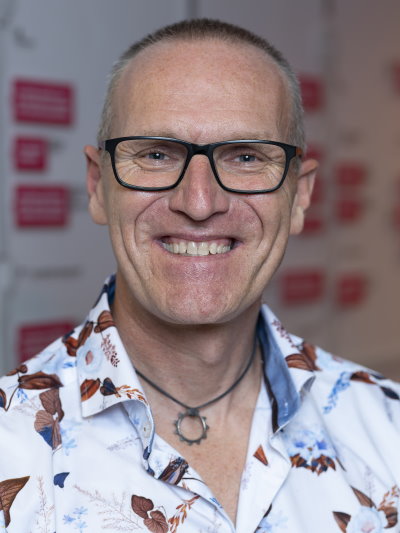
If this also fails, ASML and Sentech will explore the sensing physics involved to develop a new sensor from the basic sensor principle. While engineers may find this a nice endeavor, itâs not ASMLâs primary objective. Creemers: âOur challenge is to achieve as much as possible with proven technology. Thatâs why we strive for early involvement in development projects.â To that end, the architects and engineers at ASML must have Component Management on their radar. âThen we can quickly help them get started and steer them in the right direction. That will prevent a lot of frustration.â Verstappen: âIn retrospect, it appears that the most successful projects were those in which ASML, their first-tier suppliers and Sentech were jointly involved in the sensor integration from an early key decision stage.â His colleague Sean Ram adds: âThatâs the stage where the ideal mix of the above can be achieved.â
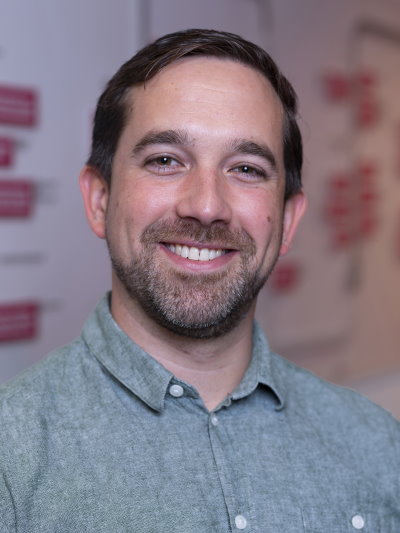
Beyond the datasheet
âWe can answer simple sensor questions ourselves, but at ASML, itâs usually not simple,â notes Creemers. âWeâll then engage in discussions with partners such as Sentech, while they can liaise with manufacturers that have the IP of the technology and make the sensors. Then, the three of us can delve deeply into the technology.â
This depth is paramount, says Ram. âWe understand the information thatâs shown in the datasheet and even beyond, to determine whether it fits ASMLâs needs and to identify the possible risks.â Creemers: âFor example, we often work within a relatively small temperature range, while sensors are specified for a range of, for example, â40 to +70 °C. In that case, we ask the manufacturer to specify the sensor for our small temperature range; usually, it then performs even better.â
Next to all the functional requirements that ASML sets, reliability is also crucial, Creemers points out. âItâs very important to our customers that we prevent downtime of our machines because of a failing sensor.â Verstappen: âWe can do many tests in the preliminary stages to validate the reliability of sensors.â Creemers: âIn addition, weâll enter into discussions with sensor manufacturers to get a feeling that weâre making the right choices QLTC-wise, judging from their knowledge and expertise.â
Roadmapping
Component Management also plays a pivotal role in future developments, Creemers concludes. âWe connect ASMLâs system architecture roadmaps to the technology roadmaps emerging from the market. For example, when our architects prescribed immersion, I started translating this into the required sensor technology. With the machine becoming wetter, for example, the flow, pressure and temperature sensors had to be resistant to demineralized water and corrosion and have a higher IP protection class. In the shift to vacuum environments, we had to deal, among other things, with strict outgassing requirements. In one case, a strong collaboration with Sentech and a preferred manufacturer enabled us to create proximity switch solutions that met the appropriate material and functional requirements.â
For roadmapping, Creemers will generally explore the market himself, call on Sentech and push new technology roadmaps to ASMLâs design community. âFor example, Sean and Peter introduced a new technology, capacitive hollow-shaft encoders, that could be of interest to us.â Ram explains: âWe also look at other markets that we serve, such as agro, aerospace and medical, where they also have to deal with challenging circumstances and high demands on cleanliness, outgassing and so on. Weâve supplied the medical market with various solutions and are now moving toward surgery robotics. As with ASML, everything must be extremely accurate and super reliable. For aerospace applications, we were already familiar with capacitive hollow-shaft encoders; we believe they also offer possibilities for the semicon industry. In this way, we facilitate cross-pollination to push each other to ever higher levels in sensor technology.â Verstappen: âAnd in supply chain collaboration as well.â
This article was written in close collaboration with Sentech. Main picture credit: Fotowerkt.nl