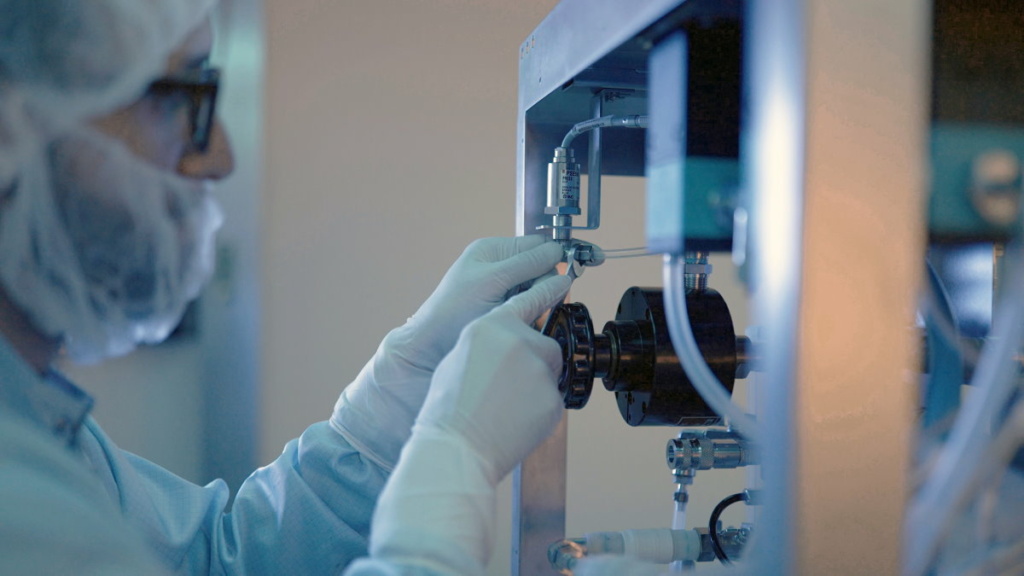
Next steps in machine conditioning
Teesing supplies products and services for the transport, control, sealing, distribution, filtration, purification and measurement of gases and liquids. This concerns products such as couplings, pipes and valves, as well as systems and high-quality assemblies in pneumatics, hydraulics, instrumentation and machine conditioning. The company was established in 1952 and now has approximately 100 employees. Headquarters are located in Rijswijk with offices in the US, Taiwan and China.
Teesing has been a supplier of ASML since the start of the litho giant as a joint venture of Philips and ASM, says key account manager Frank Bazelmans. “We already supplied products to Philips for their lithography development and were asked to continue that. In 1992, we were awarded the status of preferred supplier at ASML. Since then, we’ve undergone a significant evolution in our deliveries. It started with components related to the cooling systems, and at the beginning of this century, products and integrated assemblies for the high-purity gas distribution inside their machine were added. We’ve included our suppliers, the manufacturers of those components, in the shift toward increasingly higher requirements.” Besides products, Teesing also provides services for example in engineering, assemblies, testing and service kits.
Sustainability goals
Over the past ten years, Teesing has been supplying more and more compound products. This has everything to do with the continued growth of the ASML ecosystem including its first-tier system suppliers, explains Jurre Oorlog, corporate manager sales & marketing at Teesing. “The value chain is increasingly specializing in its core competencies. Co-makers commission us for integrated assemblies that they no longer want to make themselves. This concerns solutions for machine conditioning, such as the cooling water supply and the use of special gases. We’ve been in that business for more than fifty years; companies like ASML benefit from the application knowledge we’ve built up. Think of maintaining a constant temperature in their machine in which a large power source dissipates a lot of heat, or the use of special gases to support their technology.”
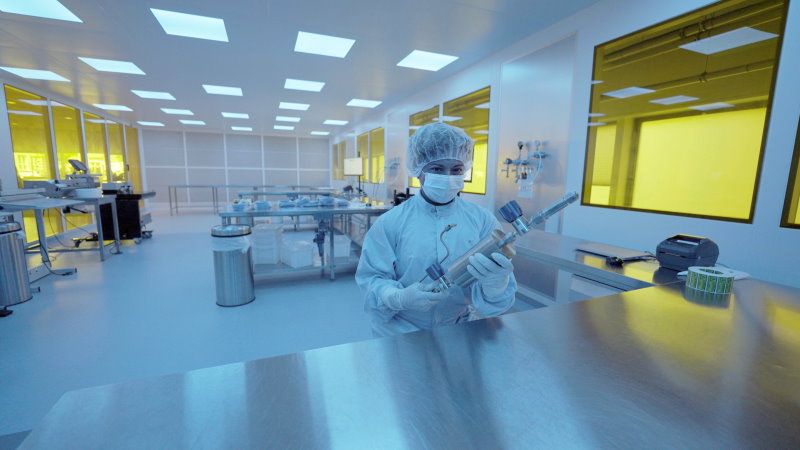
A current example of the latter is hydrogen as an addition to the gas supply in EUV machines. Hydrogen is used in the vessel where EUV light is generated from droplets of tin that are hit by a laser beam. The hydrogen flow acts as a kind of curtain that must prevent the resulting tin contamination from disrupting the process in the machine. Bazelmans: “We supply special products for filtering and flow conditioning that are used in a number of critical places inside the machine.”
A special challenge with regard to ASML’s sustainability goals is the reuse of hydrogen, Bazelmans declares. “Not yet as a process gas, but as an energy source. After all, the reaction of hydrogen and oxygen produces electrical energy – and water as a clean residual product.” Teesing has also become involved in ASML’s R4R (Return for Reuse) program. “We’ve already been asked whether our products can be used again in a machine if they’re returned. We’re now setting up a process internally to qualify products for this. First-tier suppliers are responsible for the reuse of modules, but we have the knowledge to test specific components for this.”
Build-to-print-plus
Teesing takes care of the assembly of modules according to the designs supplied by the customer – build-to-print. It also increasingly contributes to engineering itself, Bazelmans adds. “ASML and its co-makers demand that we critically review their designs. If we think something can be improved, for example to make it cheaper or more reliable, we’ll submit a proposal. We call that build-to-print-plus. Sometimes, we’re even asked to solve a problem. Then, we come up with a design ourselves and take full responsibility.”
For example, Teesing supplies complete manifolds for the distribution of gases, including valves, pressure regulators, filters and purifiers. In short, everything that’s needed for the functionality that the customer requests. “We contribute to the engineering of such a manifold and obtain the necessary products from our suppliers. Our strength is that we’re brand independent so that we can always make the best choice. If necessary, we have components made to measure. We then take care of the assembly and carry out tests. This is how we ultimately deliver tested functionality to our customer.”
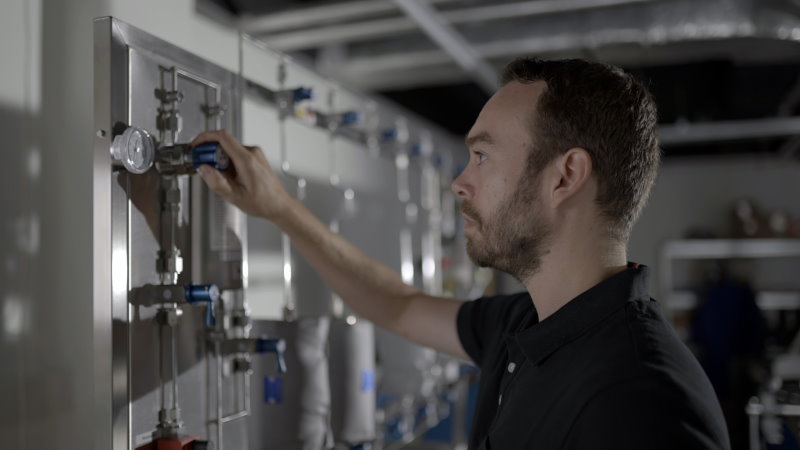
Ambitious growth target
Growth in volume and complexity means that Teesing needs more and more technological knowledge and new employees. The company has therefore drawn up a five-year plan targeting a 30 percent growth year-on-year, Oorlog states. “We’ll invest in people, resources, systems and methods for development and production. With this, we want to serve the ASML ecosystem as well as other high-tech customers.”
The 30 percent growth target is ambitious, Oorlog acknowledges. “We had to adjust our growth figure because we grew faster than expected. In a few years, we’ll reach maximum capacity at our current location. We’re therefore now looking for larger premises, where we can expand further and have more flexibility to optimally organize our activities. For example, we need more and more space for our engineering and testing activities as well as cleanroom capacity for clean assembly.”
In addition, Teesing is considering establishing separate production facilities close to customers, Oorlog concludes. “We already have offices in America and Asia for customer service and operational support because we find it important to serve our customers in local time zones and local cultures. That’s why we’re considering local production in the future. In this way, we strive to continue our contribution to the worldwide success of cutting-edge technology. We’re proud of our long-standing relationships in the ASML ecosystem.”
This article was written in close collaboration with Teesing. Main picture credit: Teesing